通過幾個模具實例,論述了改進壓鑄模具的設計在生產過程中的重要性,有時,對于模具做出的一些小小的改進,在今后的批量生產中就會帶來可觀的經濟效益。改變思路、從小事做起,在生產實踐中不斷學習和提高,使我們設計出的模具日臻完善。
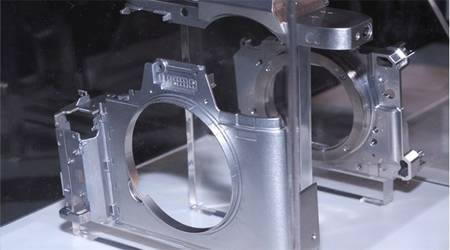
一、鑄件二次脫出,提高緩沖體鑄件精度和生產效率
如圖1所示的摩托車緩沖體鑄件,該鑄件平均壁厚2.5mm左右,機械加工后再配一個適當的鏈輪即為緩沖體組件。為保證摩托車后輪的平穩行駛,該組件裝配時,緩沖體的4個鏈輪安裝孔與中心的軸承孔之間有較高的位置度要求。
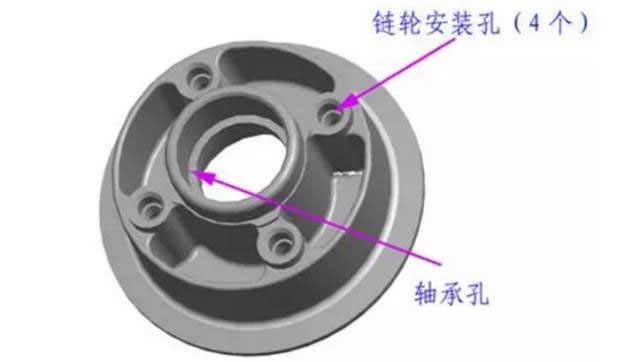
圖1 緩沖體鑄件圖
1.原有鑄件的缺陷及改進
由圖1可以看出,因鑄件結構所限,鑄件在脫模時的抱緊力較大,為順利地脫模,早期的壓鑄模具的頂桿設計如圖2所示。為放置頂桿,鑄件上的4個鏈輪安裝孔的底孔便無法在模具上做出,需通過后續的機械加工的方式完成。但鑄件在后續的機械加工過程中,因安裝孔處壁厚較厚,鑄件的內部縮孔嚴重,嚴重影響產品質量。同時,由于螺紋安裝孔沒有底孔,對機加定位要求較高,稍有疏忽,機加后的鑄件則位置度超差,無法滿足使用要求,且生產效率極低,滿足不了批量供貨的需求。
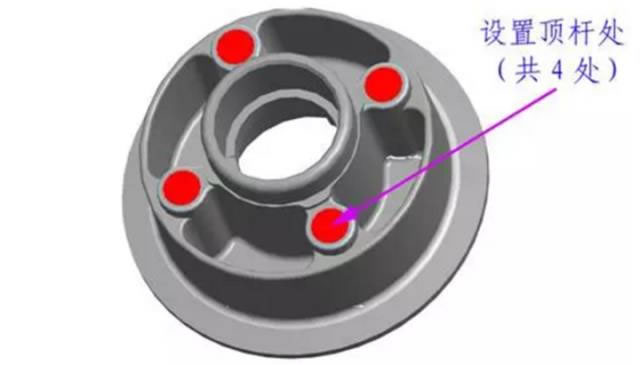
圖2 原有鑄件示意圖
為從根本上解決這個問題,就必須對壓鑄模具在結構上做出改進和提高,螺紋安裝孔有必要在毛坯件上做出底孔,要在毛坯上做出底孔,就必須改變頂出桿的位置。
經過分析討論,決定將頂出位置更改為如圖3所示的部位,同時由原來的4根頂桿增加到8根。
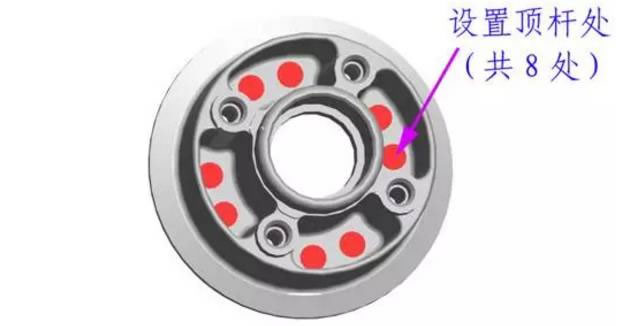
圖3 改進后的鑄件示意圖
生產過程中發現,由于頂桿所在位置鑄件壁厚較薄,加之鑄件抱緊力較大,鑄件不能順利地被頂出,時常會發生鑄件頂出時底面被頂穿的現象,造成鑄件報廢。
2.新設計模具的提高
要想解決這個新問題,勢必要增加頂桿數量或減小鑄件的抱緊力,由于位置所限,再想增加頂桿數量已不可能,只能從減小鑄件的抱緊力上下功夫。
根據模具結構,我們決定通過讓鑄件二次脫模的方式脫出,來分減第一次所需的頂出力。具體方案為:
將動模中芯的尾部臺階做到6 mm厚,動模型芯上的安裝孔的深度做到10 mm(如圖4 所示),開模時,動模中芯隨壓鑄件一起向前運動4 mm,完成第一次脫模。此后,頂出板繼續頂出,壓鑄件再從動模中芯上脫出,完成第二次脫模。通過兩次脫模,減少了每次脫模的力量,可順利完成壓鑄件的脫出。
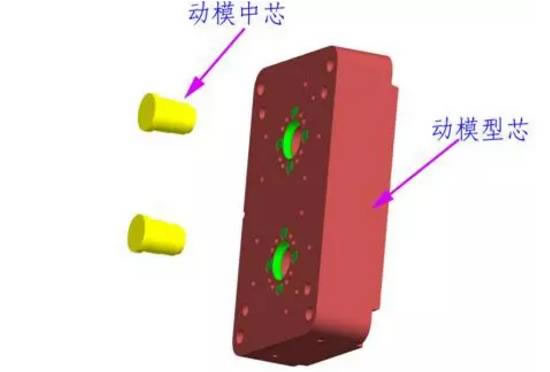
圖4 緩沖體動模芯
解決了壓鑄件的脫模問題,還需要在下一循環中使定模中芯準確復位,否則鑄件尺寸將發生變化,質量得不到保證。對于定模中芯的復位問題可利用模具自身的結構來完成,該模具動模中芯和定模中芯是相貼合的,合模時,依靠定模中芯將頂出時跟出的動模中芯推回,即可使其準確復位。
通過上述模具結構的改善,從根本上解決了緩沖體壓鑄件沒有鏈輪安裝孔底孔,后續加工難度大的問題,降低了廢品率,大大提高了后續機械加工的生產效率。
二、增加排氣通道,穩定鑲件尺寸
如圖5所示的減速器殼體鑄件,該產品共有5件嵌件,且大部分一次成形,不再進行二次加工,對嵌件的尺寸要求較嚴。
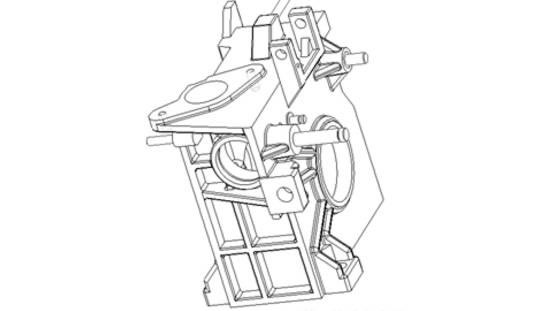
圖5 減速器殼體鑄件
在生產過程中發現,產品的嵌件長短不一,且不合格品分布完全沒有規律性,每個操作工、每個班次都存在有大批的不合格品。經過分析可能原因如下:
- (1)模具上嵌件安裝底孔深度不合格;
- (2)操作者未將嵌件安裝到位;
- (3)壓鑄機合模時因震動使嵌件脫出;
- (4)嵌件本身尺寸不合格導致安不到位。
經過現場排查,模具上的安裝底孔深度和孔徑都符合圖樣要求的尺寸;嵌件尺寸也完全符合圖樣規定的公差;據操作者反映每次嵌件都安裝到位,就是干出的產品尺寸長短不一,壓機震動的原因似乎也站不住腳。通過深入的了解,我們發現了一個不起眼的問題,操作工反應:嵌件安裝時似乎有彈性,不易一下安裝到位。
根據這個現象,我們做了大量的嵌件安裝試驗,結果表明:由于模具底孔與嵌件的配合公差較小,操作者快速將嵌件安裝進去后,底孔內的空氣無法排除,形成一個空氣壓縮后的氣墊,將嵌件從安裝孔中彈出。
為解決此問題,我們將模具安裝孔的底部增加了一個排氣通道,安嵌件時使孔內的空氣能從此通道順利排出,杜絕了類似問題的發生,保證了產品質量。
三、改進模具結構,防止輪轂模具局部開裂
如圖6所示的輪轂產品,是摩托車上一個常用的零部件,過去一段時期,輪轂壓鑄模具常在短期內發生局部龜裂(如圖6所示的模具龜裂部位),嚴重的影響了鑄件的外觀質量。
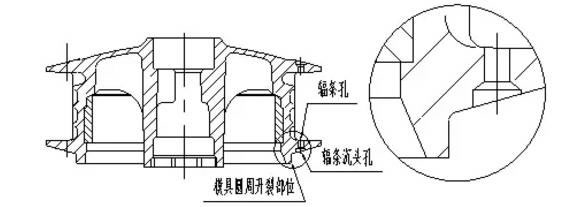
圖6 100前輪轂示意圖
為改善鑄件的質量,我們對輪轂模具做了認真的分析,模具短期龜裂的主要原因有:
- (1)模具材料及熱處理;
- (2)模具結構設計不當;
- (3)模具使用不當,缺乏必要的維護;
- (4)脫模劑使用不當。
從模具結構上我們可以看到:圓周上的18個輻條孔及輻條沉頭孔是由整體的18個小型芯成形的,這樣,模具的動模、定模方芯便可以采用車床加工的方式完成,降低了模具加工難度。但是,這種結構從動模芯上來看,就造成了模具上18個輻條孔芯周圍局部厚度僅有2mm左右。參見圖7局部放大所示,圖示點狀區域是原有模具輻條小芯,如果將此區域與動模方芯一次成形,僅用活動型芯成形輻條孔,那么此處的模具壁厚將增加到4mm左右,雖然增加了模具的加工難度,但模具強度將會大大提高。在隨后的模具制作中,我們改進了模具結構設計,用圖8b所示的芯子取代了原有的圖8a所示的輻條孔芯子,后期的輪轂模具基本上避免了在此處發生的早期龜裂現象。
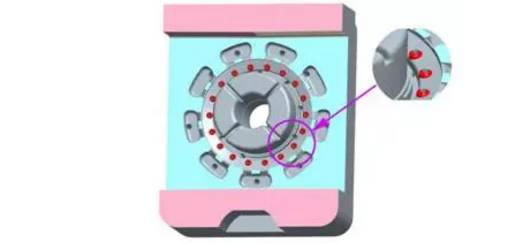
圖7 輪轂模具動模芯
圖8 型芯的更改示意圖
四、增加工藝芯子,降低右箱體粘模時的維修難度
摩托車100型右曲軸箱體(如圖9所示),在孔1附近有較多的凹槽,生產中極易發生產品件粘定模現象,且粘模后不易從定模中取出。每次粘模都浪費了大量的人力和物力來進行處理;由于受到圖樣尺寸所限,此處不能依據常規方法即加大脫模斜度的方式來解決。除對模具進行了適當的處理以減少粘模外,如何在粘模發生時盡快地取出粘模的鑄件,成了要解決的一個主要問題。
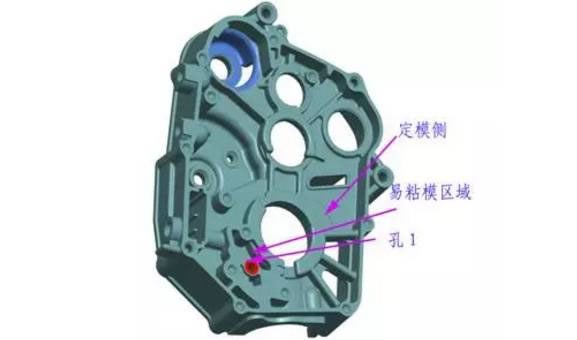
圖9 右曲軸箱體
通過對模具分析發現:孔1是由動模上的型芯來成形的,而粘模發生時,此型芯已從鑄件中脫出,如果在孔1對應的定模側增加一個工藝型芯(如圖9所示),粘模時可通過孔1將此型芯敲出,之后利用此孔便能輕松的將粘模區域的鑄件從定模中敲出。
通過上述實例分析,我們可以看出,如果在模具設計初期,設計人員能夠與壓鑄模使用廠家進行深入的溝通,針對原有模具使用中的一些問題進行有目的的探討,力爭在新的模具設計制作中加以改進,對于后續的模具的使用維護、鑄件的批量生產,以及后續加工都大有裨益。
作者:崔愛軍
來源:中鑄科技全鋅網壓鑄技術服務(ID:yazhuzhuanjia)