工廠在實施精益生產方式時,不要急功近利,要著眼長遠打算。改善無小事,只要有機會就去改善,一步一步腳踏實地,見微知著,精益從小事著手。
1.管理決策以長期理念為基礎,即使因此而犧牲短期利益
實施精益生產也一樣,要有一個長期發展戰略規劃。因為精益生產不可能一蹴而就。日本豐田汽車實行精益生產也是經過長期的艱苦探索。從提出了準時制的理念到成為一種先進的生產模式。
因此,在實施精益生產方式時,不要急功近利,要有長遠打算。改善無小事,只要有機會就去改善,這是本人之拙見。一步一步腳踏實地,見微知著,精益從小事著手。
2.建立無間斷的操作流程以使問題浮現
所謂無間斷的操作流程,就是連續流生產。根據單件產品生產的消費節拍(Takt)、用戶訂購產品的速度來安排生產流程,及時滿足消費者的需求。在確定生產節拍后,要分析流程圖,哪些流程有附加價值,哪些流程無附加價值,減少無附加價值的流程,以提高過程績效。
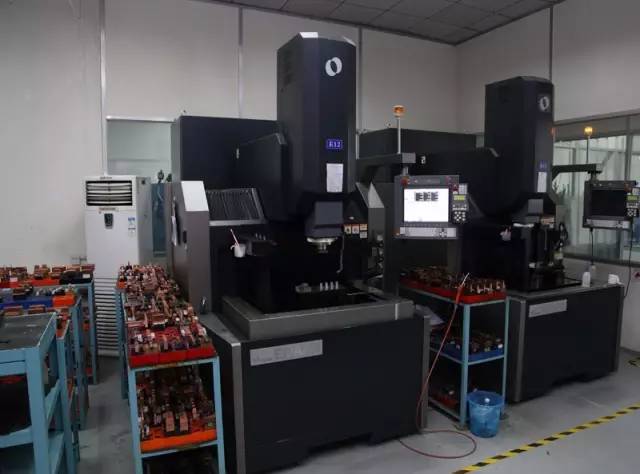
3.實行拉式生產制度以避免生產過剩
所謂拉式(Pull)生產制度是以客戶需求為驅動的生產制度。以客戶訂單量為依據,確定生產計劃和日程安排。而實現拉式生產制度的基本方式就是看板管理(Kanban)。看板是工廠和供應商都與用戶的節拍時間保持同步的一種方法。
4.使工作負荷水準穩定(生產均衡化)
為使工作負荷水準穩定,要進行線平衡分析,盡量使各工序平衡和單件產品生產時間相匹配。
5.建立立即暫停以解決問題,從一開始就重視品質管理的文化
將品質意識貫徹到每一個人員的心中,開展TQC活動,提合理化建議;利用PDCA循環,持續改善過程品質。
6.工作的標準化是持續改進與授權
做好標準化工作,持續改進過程品質,作為程序標準化,提高工作效率和流程效率。
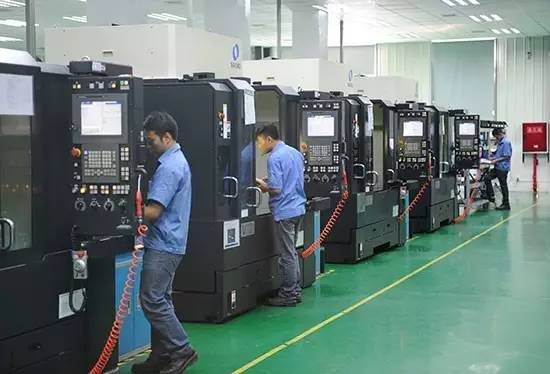
7.運用目視管理使問題無處隱藏
通過5S制度的建立,使辦公室和工廠一塵不染,機器上無灰塵、油污,無碎片或臟物,建立一流清新的工作環境,營造積極向上的企業文化。目視管理使物品標識清晰,看板管理使一目了然。
8.使用可靠的,已充分驗證的技術以協助員工及生產流程
通過不斷開發新產品,運用先進的管理技術,提高企業的自主創新能力,如進行六個西格瑪設計,提高產品質量和可制造性(DFM)、可靠性。
9.把徹底了解且擁護公司理念的員工培養成領導者,使他們能教導其他員工
加強多能工的培養,使每一位員工都具有協助小組成員員工作的能力。同時要培養領導團隊工作的能力。
10.培養與發展信奉公司理念的杰出人才與團隊
發揚團體合作精神,培養優秀人才,解決企業中的難點和重點問題;組建跨功能團體,優勢互補,維持企業的有效運作。
11.重視企業伙伴與供應商網絡,激勵并助其改進
加強供應鏈管理,重視與供應商的協作關系,與供應商形成利益共同體。
12.親臨現場查看以徹底解決問題(現場現物)
加強現場管理,執行現場、現物、現實原則,第一時間徹底解決現場工作中的實際問題。管理者要身先士卒,事必躬親,沒有到現場就沒有發言權。13.不急于決策,以共識為基礎,徹底考慮所有可能的選擇,并快速執行決策
管理者盡量進行群體決策,充分考慮大家的意見,大家定了決策,就要一步到位去執行;不但要有決策力,更要有執行力。
14.通過不斷省思與持續改進使企業成為一個學習型組織
要建立持續改善、不斷創新、努力學習、追求卓越的企業文化,只有不斷變革、不斷學習,才能跟上時代的發展步伐。精益生產也在不斷向前發展,因此要努力學習先進公司的生產模式,使企業成為一個學習型的組織。