設(shè)計(jì)porcerax II排氣鋼時(shí),應(yīng)考慮以下準(zhǔn)則:
1.使用的樹脂
根據(jù)成型過(guò)程中的氣體排放量或殘留評(píng)估使用7或20微米孔徑。如7微米小氣孔新東透氣鋼,在ABS、聚丙烯樹脂、軟型聚氯乙烯、聚乙烯、聚丙烯、聚氨酯、苯乙烯中表現(xiàn)良好,對(duì)于低粘度或滑石粉填充樹脂,它可能需要有一個(gè)自動(dòng)化的系統(tǒng)反向氣流互射清除毛孔后的雜質(zhì),硬質(zhì)PVC樹脂也適用,但隨著被氣體長(zhǎng)期腐蝕,透氣孔會(huì)堵塞,如果工件不需要重復(fù)利用,這仍然是一個(gè)可行方案。
在排氣量非常多時(shí),建議采用20微米孔徑的新東新東透氣鋼。20微米慪氣剛的開發(fā)是為了滿足研磨后直接使用,經(jīng)過(guò)正確的研磨,20微米新東透氣鋼留下的氣孔是部分開放(約40-50%)。然而,使用20微米孔徑的新東透氣鋼,并保持20微米孔徑,通過(guò)電火花加工或研磨拋光后,透氣性比7微米更好,但是它也將堵塞得更快。
2.排氣區(qū)域的面積大小
建議核心腔面積至少10%是PORCERAX II新東透氣鋼,以確保穩(wěn)定的排氣。雖然這并非總是必要的,它是要記住,在模芯和腔區(qū)域中的使用面積,帶來(lái)的較低的背壓是重要的。由于較大的表面積,該新東透氣鋼工件不需要經(jīng)常清洗薄的PORCERAX新東透氣鋼透氣性能會(huì)更好,不過(guò)要注意PORCERAXⅡ新東透氣鋼的機(jī)械性能。太薄的透氣鋼零件可能無(wú)法承受注塑壓力。
3.表面光潔度要求
由于大多數(shù)的新東透氣鋼都是應(yīng)用在模芯側(cè)面來(lái)解決,如果電火花的光潔度可以接受,排氣性能會(huì)是最高的。如果有更高的光潔度要求,研磨拋光的表面將提供一個(gè)最好的排氣表面。重要的是,如果新東透氣鋼在模具的模腔側(cè)使用,光澤度就會(huì)受到嚴(yán)重降低(#9到#2-3與PP),所以需要考慮是否匹配設(shè)計(jì)要求。
4.透氣鋼的各種安裝槽設(shè)計(jì)圖紙

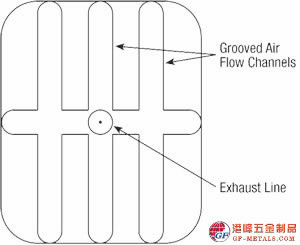
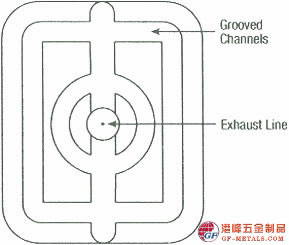
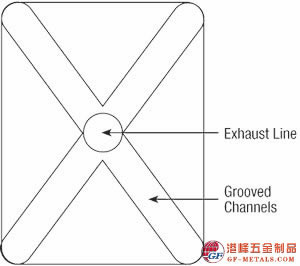
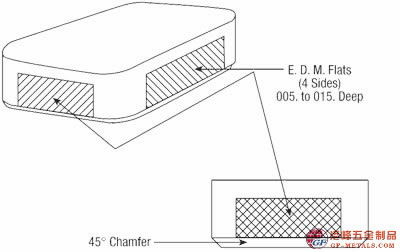
Porcerax II
Design Guidelines
When designing for Porcerax II venting steel, the following guidelines should be considered:
Resins Used
Depending on the emissions or gas residue given off during the molding process, the molder will have to evaluate whether to use a 7 or 20-micron pore size. Resins such as ABS, polypropylene, soft type PVC, polyethylene, acrylic, polyurethane, and styrene work very well with a 7-micron pore size. For low viscosity or talc-filled resins, it may be necessary to have an automated system reverse the airflow after each shot to purge the impurities from the pores. Rigid PVC resins will work, but only until the corrosive gases close the pores. This can still be a feasible method if disposable inserts are used. Where extreme venting is needed, a 20-micron pore size is recommended. The 20-micron grade was developed to be used with a milled finish. When milled properly this process with the 20-micron material leaves a pore that is partially open (about 40-50 %). However, using the 20-micron pore size material and maintaining the 20-micron pore size, by EDM or polishing after milling, will vent better than 7-micron, but it will also clog faster.
Size of Area to be Vented
The producing mill recommends that at least 10% of the core and cavity area be Porcerax II to insure proper venting. While this is not always possible, it is important to remember that the more square inches used in the core and cavity area, the lower the back pressure will be in the cavity. Due to the larger surface area, the insert will not require cleaning as often as a smaller piece. If Porcerax II is used as a core or cavity half, instead of as an insert, there may not be a need for parting line vents.
Note:The thinner the Porcerax or the shorter the distance air has to travel to the exhaust
line the better the venting will be. Keep in mind the physical properties of Porcerax II.
Note:Porcerax is typically inserted on the core side of the mold in the problem area in
order to hide insert lines.
Surface Finish Requirements
Since most applications can be addressed using inserted pieces on the core side, an EDM finish is acceptable and will vent better than any other surface finish. Should EDM be impractical, a stoned or polished surface will provide the next best venting surface. It is important to remember that if the venting steel is used on the cavity side of a mold, the gloss level will be severely reduced (#9 to a #2-3 with PP), so matching should be considered.
If a low gloss level on a textured part is desired, it can be accomplished with the 7-micron Porcerax II. Certain procedures must be followed to prevent the possible, irreversible damage to the internal pore structure of the material. The texturing house selected for this procedure must be advised that they will be texturing porous, venting steel. The pores must be thoroughly cleaned and sealed prior to texturing. This insures the acid used to etch the surface does not run through the material corroding the interior structure. Performed properly, texturing Porcerax II will give the molder an unmatched finish in terms of definition.
Slide/Lifter Applications
Porcerax II can be used in slide or lifter applications. However, it is important to consider lubrication requirements on such a design. Lubricants will, in all likelihood, reduce or eliminate permeability in areas that come into contact with Porcerax II.
本文出自*港峰公司*,轉(zhuǎn)載請(qǐng)注明出處!